In the spring, our guest blogger Bill Sweeney from Coastal Forest Products wrote about a big project in York, Maine (see part 1 and part 2 of this series). This MDU condo project, is now well into the Plumbing, Electrical and HVAC installation. Bill describes it for us
Update on construction at York Beach Residence Club project in York, Main – By Bill Sweeney
The York Beach Residence Club is a big, 4-story 25 unit multi-use deluxe condo development, eagerly anticipated by the local community. It replaces a legendary but decrepit building in a prime location near the beach. 5 months into construction, it looks like it will be finished 2 to 3 weeks earlier than expected, this fall. This happens to be is great news for a project that actually started out 2 to 3 weeks late.
I would attribute the recouped time to faster than expected framing, and particularly to the use of the open joist TRIFORCE®. Thanks to their lightness, the joists were very quickly moved into place. Had much heavier plated Truss Joists been used, the process of moving them to the crane, hoisting them and setting them into place would have been much more time consuming/labor intensive.
Mechanical installation
Now that we are well into the mechanical installation, TRIFORCE® is again proving how easy it is to work with.
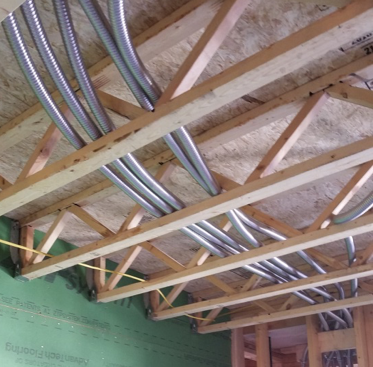
For example, one of the tricky things about running electrical wiring through Truss Joists is avoiding the sharp edges of the metal plates, which can strip wires. You’ll notice that the wiring on the left has corrugated sheathing. It almost seems designed to get caught on Truss Joist plates. Obviously, this won’t happen with the TRIFORCE®.
In this picture of the plumbing, you can see how easy it is to use a laser in one direction or another to ensure the required slope. This would have involved so much more work had I-joists been used. With the I-joist, holes have to be cut very precisely to have a smooth slope.
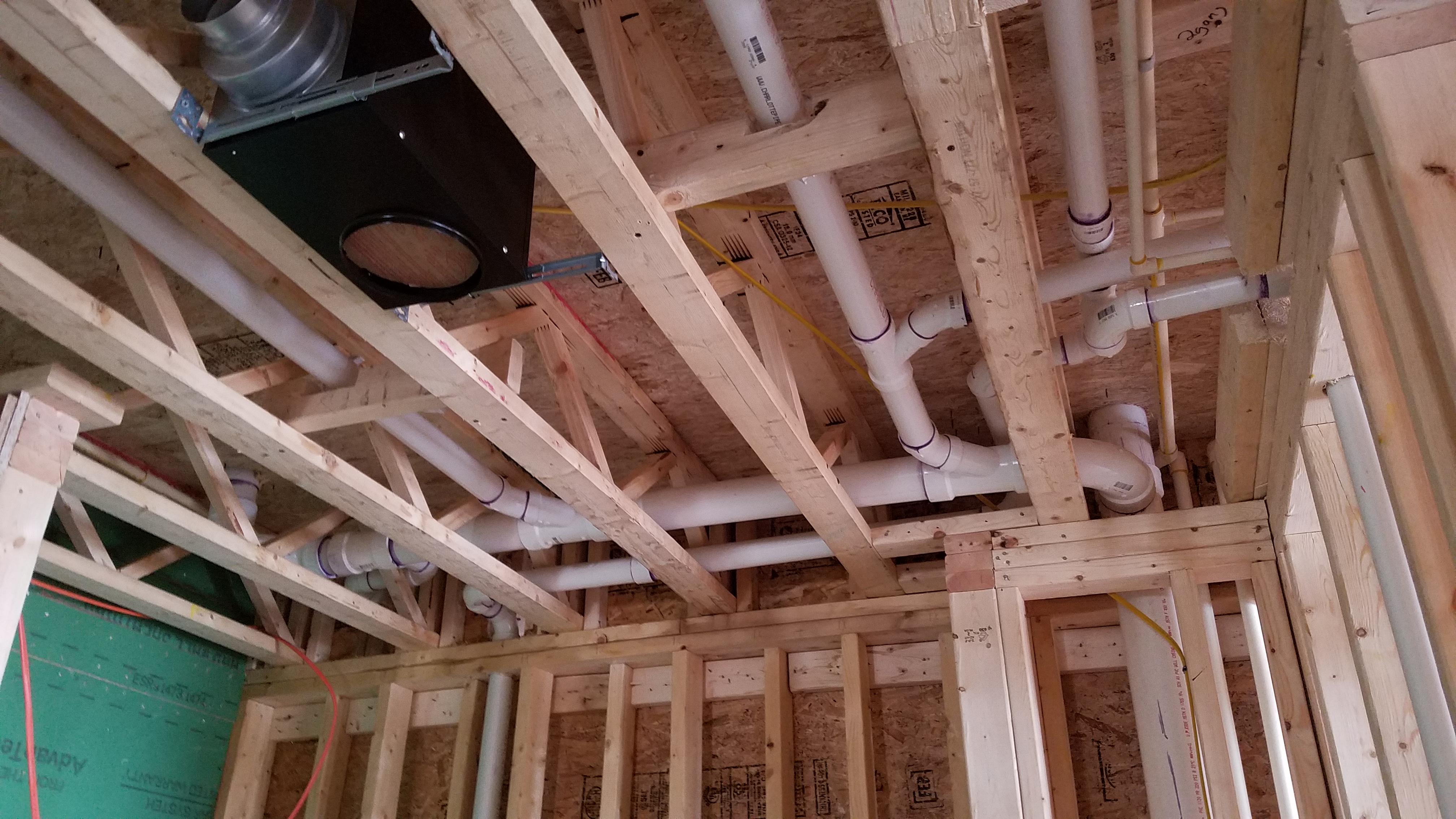
Here below is an 8-inch forced-air duct running at the edge of the room. Certainly, a hole that size would have been unacceptable in that location on an I-Joist.
In terms of repairs, it has been minimal. A plumber had to cut into the joist top chord at four locations and all it took was a simple repair detail to fix it.
It’s been a pleasure seeing the advantages of the open joist TRIFORCE® come to life on the York Beach Residence Club project. Needless to say that in such a clean and open environment, plumbing, electrical and HVAC installation just hums along.
Who knows, we might catch up a few more days in the process.
Want to know more about this particular project?
We’ve throughly documented it before in a three-part series: Part 1, Part 2, Part 3
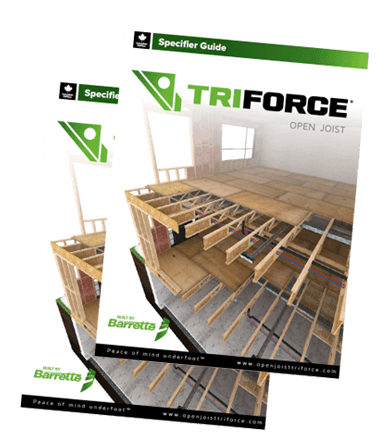
Bill Sweeney
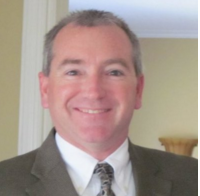