Find out why individually testing joists helps to ensure quality and customer satisfaction. It prevents many types of inconveniences and improves performance.
This blog will explain why individually testing joists is crucial to ensure maximum quality. Not only does this process help to identify defects early but will improve product reliability and, by the same token, customer satisfaction. Let’s see how it can prevent all types of inconveniences and improve overall joist performance.
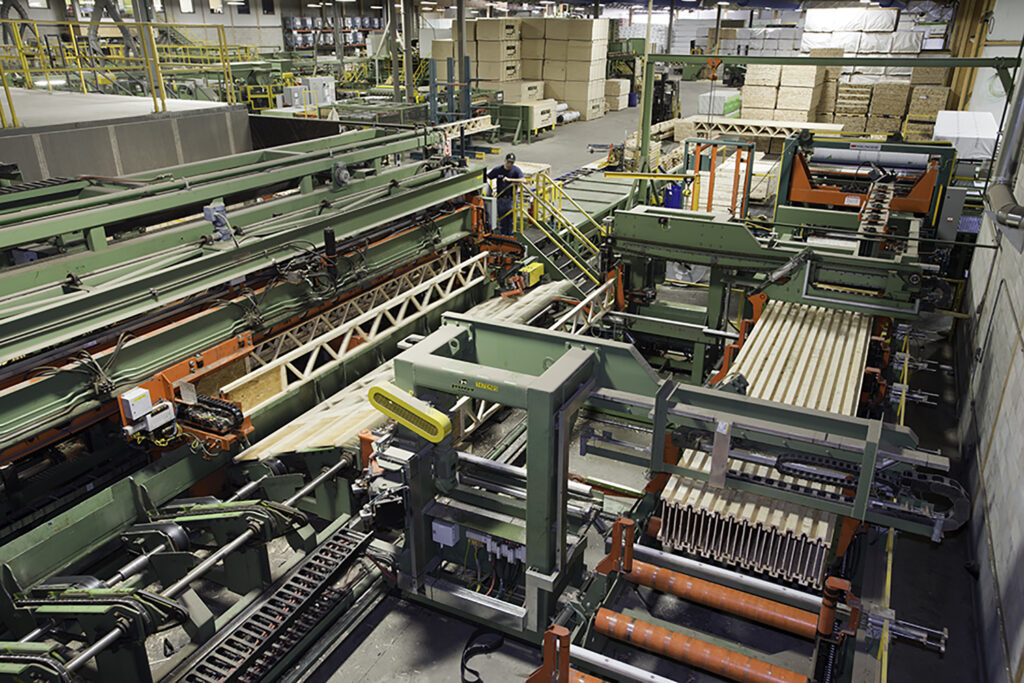
Every industry wants to offer its customers superior quality standards for their product, so do we! We have therefore set-up specific policies and procedures to ensure excellent quality control. These rigorous processes characterize the excellent quality of TRIFORCE® joists, as each one is individually tested.
5 reasons why good production supervision is so important:
1) Good quality control ensures ongoing customer satisfaction, and high quality standards help build customer trust and a solid reputation in the market.
2) There is a clear link with cost reduction. As all imperfections, defects or other anomalies are detected at an early stage in the manufacturing process.
3) Ensures compliance with regulations: Engineered wood products must be certified by official bodies to guarantee the well-being and safety of customers.
4) Increase of the efficiency: By monitoring production quality, it is possible to upgrade certain areas of the fabrication by collecting data on a daily basis. This will contribute to a continuous improvement.
5) Improved teamwork: good quality control results in employees that are more responsible, more motivated, more committed, and feel more involved in the company’s success.
What does this testing process involve?
Once the joist adhesive is fully cured, all joists over 10 feet are conveyed to the inline load test machine. Each joist is visually inspected and mechanically tested. This test is performed in-line to ensure that only premium products are packed and shipped.
All tested joists will then make their way to the stacking and bundling machines. At this point, sampling for additional quality control assurances will occur.
Quality control personnel will continually verify compliance of each bundle. The bundles are then conveyed to the banding and wrapping station. Finally, all individual bundles are identified with the length, series, and depths for customer and inventory purposes.
Only verified joists are delivered to the construction site, ensuring builders’ peace of mind. Since each TRIFORCE® joist is tested, we know that they will meet the required safety standards and we can be confident that they are capable of supporting the expected loads they are designed for. This ensures the safety and the durability of the structure.
The role of robotics in testing and manufacturing TRIFORCE® joists
Manufactured in a state-of-the-art facility using fully robotic production, each TRIFORCE® open joist is guaranteed to be an exceptionally accurate end product.
This method of proceeding reflects the technological evolution of TRIFORCE® manufacturing through the years. Robotization brings significant benefits in terms of efficiency, precision and quality.
Here are 5 examples:
1) Robotization reduces human error: By relying on robots for production tasks, the potential for human error is significantly reduced. Robots operate with precision and consistency. They minimize variations in the manufacturing process that can lead to defects or inconsistencies in the final product. This ensures that each joist produced meets the exact specifications and quality standards.
2) Robot programming ensures strong, durable connections between components. Thanks to this programming, engineers can configure robot sensors and actuators, enabling them to interact with their environment in a precise and reliable way.
3) Sensor-equipped systems for joist inspection, for better quality control. Sensors can be set to measure joist height, width, length or surface finish to ensure that they meet the required specifications.
4) Greater flexibility: Able to quickly adjust production to different desired heights. For example, robots can be programmed to adjust the position of their cutting tools to suit different joist heights. This flexibility optimizes production, avoiding downtime and manual adjustments.
5) Better optimization of materials, resulting in reduced waste and cost savings.
In summary, testing joists individually is essential for ensuring durability, safety, energy efficiency, aesthetics, customer satisfaction, cost reduction and sustainability.
Our way to modernize the construction industry
This process contributes to modernizing and improving the efficiency of the construction industry. So you can be sure that your engineered wood floor system is of the highest quality, meets your needs and delivers reliable, long-lasting performance.
By putting quality first, TRIFORCE® joists can achieve long-term value and success. Also, it helps maintain a competitive edge in the market, so it is a wise decision that pays off.
To learn more about TRIFORCE® open joist floor system, take a look at our spec guide:
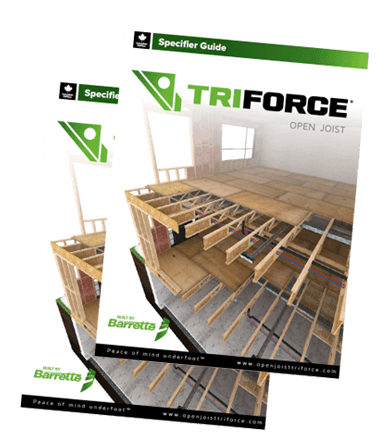