The fact that TRIFORCE® joists are assembled with “finger joints” was certainly breakthrough news in the world of engineered building components. But the breakthrough was about the application for joist manufacturing rather than the actual joinery process itself. Versions of finger-like joinery have been responsible for strong things for thousands of years. The Egyptians and the Romans constructed items using strong “box joints”. And “comb joints”, employing the same concept, have benefitted artisans for centuries.
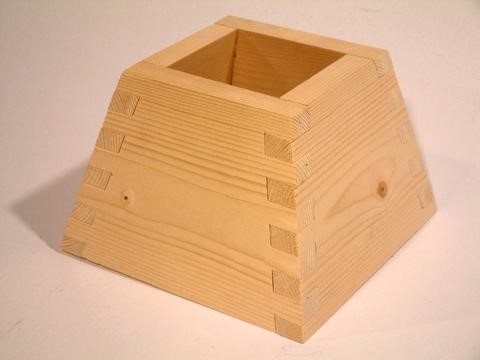
Why has this type of joinery survived so long and why is it relevant today? In one word: strength. The interlocking “tines” of these joints perform as a connective reinforcement significantly stronger than that of a “butt” joint or a “lap” joint. Multiple connection points are superior to single-plane connections.
Taking Advantage
In the late 1980’s, Canadian truss manufacturer Paul Lemyre recognized the potential of using finger joinery to improve building components, specifically floor trusses. Along with some expert wood engineers, he explored the use of adhesives and how they could enhance wood-to-wood finger joint connections. After extensive development and testing, Paul introduced a new, stronger all-wood floor truss called OPEN JOIST 2000™. It was assembled entirely with glued, finger-joint connections.
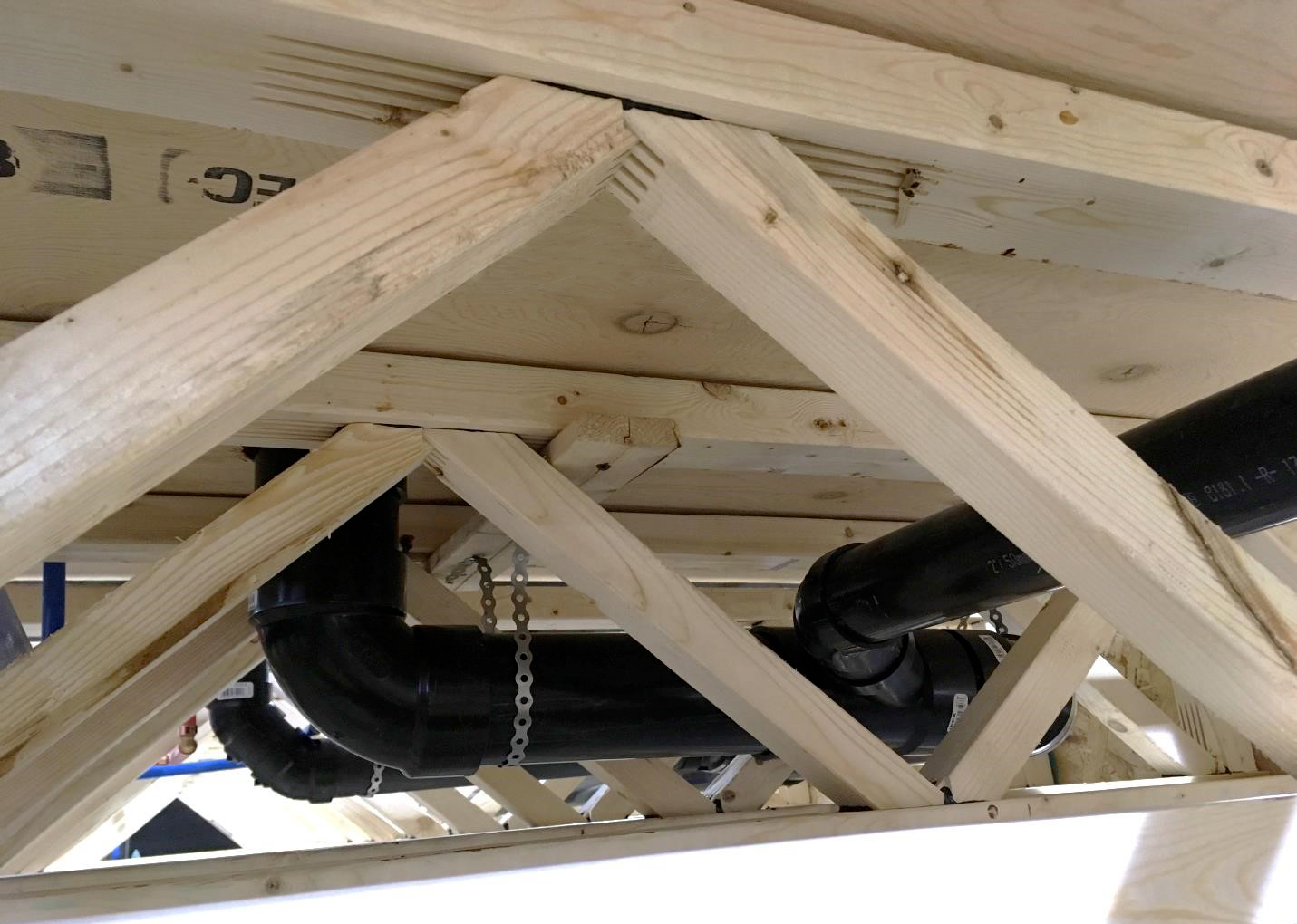
That product is the predecessor to open joist TRIFORCE®… the product being manufactured today by Barrette Structural Distribution using the same finger-joint/adhesive connections.
A Successful Marriage
TRIFORCE® owes its strength to this innovative assembly method. An examination of the milled connection areas of TRIFORCE® joist components reveals multiple deep fingers. The configuration of these fingers allows for the maximum amount of adhesive in a confined area. The glued surface is optimized, producing a stronger connection than a metal pressed-on plate. That connection is also more resilient than plated assemblies, with the ability to recover from overload situations.
The TRIFORCE® robotic assembly process employs quality checks to ensure accurate milling and orientation of finger jointed components. This guarantees that joist connections perform to maximum capacity.
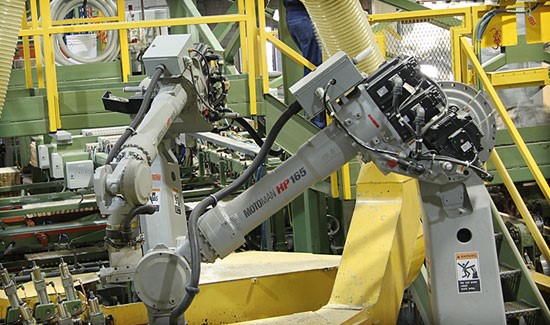
In addition to superior strength, TRIFORCE® offers benefits through the performance of its adhesive. As a standard of the engineered wood products industry, TRIFORCE®’s glue is stable, waterproof and has a higher burn temperature than wood. It’s the perfect partner for finger joints, resulting in a top tier engineered floor framing component.
TRIFORCE® wood-to-wood finger joints are the foundation for “peace of mind underfoot”.
This Truss Product is interesting. Is there a manufacturer/supplier here in the Pacific Northwest Area. Seattle-Tacoma?
If so, would there be a chance to have a lunch and learn gathering to learn more with about 10 people to attend. I’m one of several members of the American Institute of Building Designers, AIBD. We have a local Chapter of architects and building designers.
I also teach at the local college residential design.
Hello Lynn,
First of all, I’d like to thank you for your interest in our open joist.
Unfortunately, there is no supplier yet in the Pacific Northwest Area. You can have a look at our sales channel online at:
Dealers and Distributors
Do not hesitate to call 1 800 263-7265 for more details about our channel expansion and our services.
Looking forward meeting you at an upcoming AIBD event!
Best regards,
Caroline