1) Joist Repair Needed
Recently, a TRIFORCE® representative was called to a construction site because the GC had discovered a cracked bottom chord on one of the installed TRIFORCE® joists (see photo above). The cause of the damage was a mystery and no one was taking responsibility.
What could have happened? First… we know what didn’t happen. The joist did not leave Barrette Structural Distribution’s TRIFORCE® factory in this condition. An automated assembly process with visual monitors would never have allowed a joist chord with this condition to proceed through the line. Then, Quality Control measures at other checkpoints would have backed up the monitors. And, once made, the joist was protectively bundled for storage and shipment.
Transfer to the hands of others puts joists in jeopardy. During unloading, a misaligned fork might have pierced a joist. An entire bundle of TRIFORCE® joists might be dropped. Other materials might topple onto joists stored at the site. A concentrated area of a floor system might be highly overloaded with subfloor material or gypsum boards. And, there are often “mystery” causes. Regardless, a repair is needed.
In the case of the cracked bottom chord, this TRIFORCE® common repair detail came to the rescue:
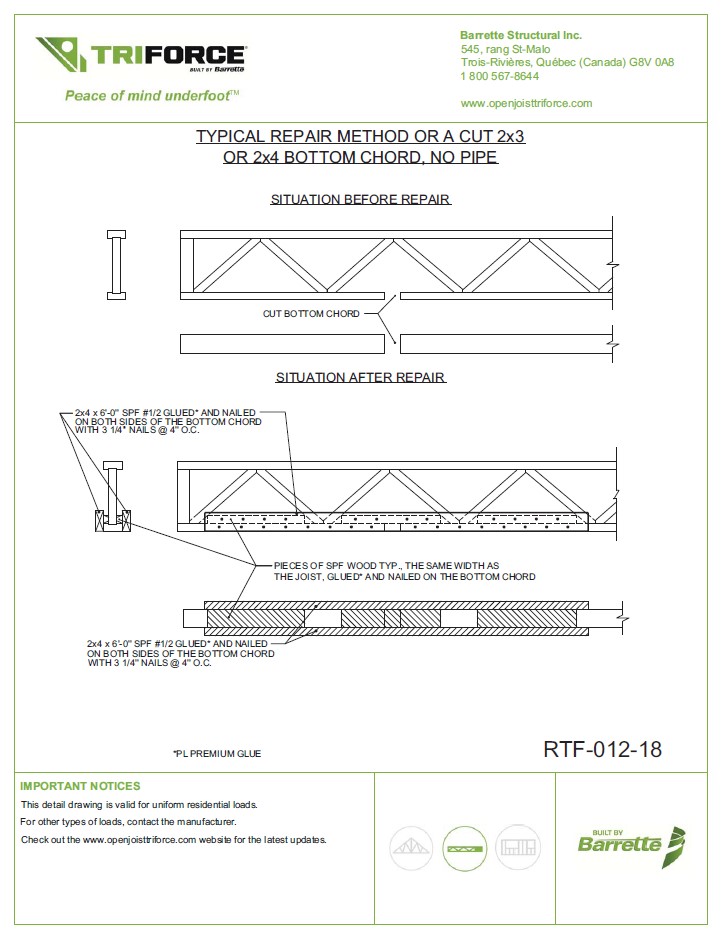
More typical repair details at: https://www.openjoisttriforce.com/open-joist-triforce/common-repairs/
2) Improper Strongback Installation
Another look at the photo above shows the strongback bridging (running perpendicular to the joists) is not installed as specified. Here, the wide flat side of the 2X is attached to the joist’s bottom chord. This does not contribute to the solid performance of the TRIFORCE® joist as effectively as a strongback installed on its side with the smaller 1-1/2” dimension attached to the bottom chord.
We recommend the following installation for best results:
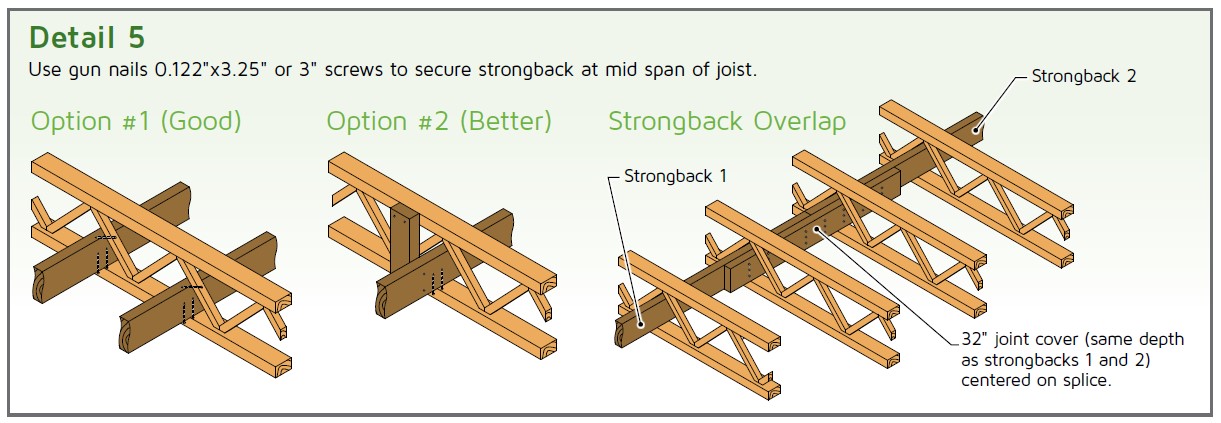
Strongback bridging is an excellent and inexpensive way to improve the overall rigidity of the floor system and eliminate vibration. It serves to make the floor more comfortable for those living and working in a structure. Strongbacks can be altered to allow HVAC installations as long as three (3) consecutive joists are attached.
With these two job site fixes, a TRIFORCE® floor system was repaired properly and enhanced for performance.
If you’d like to know more about the TRIFORCE® product, download our Spec Guide or contact us. We’ll be happy to help.
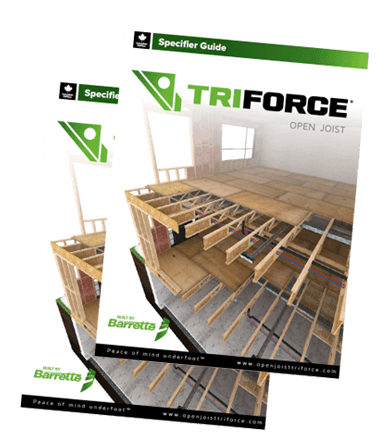
I like the no-nonsense tone of your commentary. Unless the installer
was a rookie with zwro knowledgw and/or experiencee, there is no
legitimate excuse for whatever lead to this sort of damage.
As you know, it requires a whole bundle of stress to shear a “strong-back”, regardless of how it may or may not be properly installed. I am puzzled regarding the amount of stress required to result in a shearing failure like
the picture indicates.
Please publish or e*mail me the circumstances under which this occured.
Regards,
Mike Carson, President
Temple Management (developers in the Orlando area)
Thank you Mike for following us on the TRIFORCE blog.
To answer your question, this article covers two different issues that are not related to each other. The damage is related to the bottom chord of the joist while the strongback has simply been improperly installed. Regarding the cause of the damage, we cannot pinpoint that, but the article points out four possible reasons that might have occurred.
Your picture and the damage you describe do not at all match the fix you are putting forth. Not even close.
Paul DeBaggis
Certified Building Official
Thank you Paul for your comment.
The damage is so significant that we consider it as a cut bottom chord. This is why, in this particular case, we suggest the common repair RTF-012-18 as per image above.
It’s amusing to me to see how much effort (and writing) went into this article to try to push the blame down the line. All points raised don’t prove at all that the joist didn’t leave the factory already cracked… visual QA steps in production don’t guarantee to 100% that this could ever happen.
It’s obvious the author is emotionally compromised and putting blame is cheap when the article’s title is about joist repair.
Perhaps it should be called the “blame game”?
Hello Charles,
We are sincerely sorry this was the way the article was perceived.
As with any other project, our team, as well as the distributors and/or builders we do business with, worked towards finding a solution for this particular situation. It isn’t about blaming anyone — rather, the intent was to share a list of the Don’ts (ex: incompletely built floor system highly overloaded with subfloor material or gypsum boards) and prevent it from happening in the future.
As for joists leaving the factory already cracked, rest assured we do everything to minimize the risk of having damaged joists shipped to the job site. This is what engineered wood is all about, right? Every single joist is inspected and tested prior to shipping. This is not only done by visual check points, but mainly by robots using precise sensors that test and measure a multitude of criteria. Besides, our processes are reviewed and our products are tested on a regular basis by an independent third party to ensure we deliver the quality we promise. I’m sure you will enjoy reading this blog post on that particular subject: https://www.openjoisttriforce.com/open-joist-triforce-quality-control-a-cut-way-above/
And please feel free to contact our experts if you would like to know more about our stringent quality control.
When something like this happens, finding the cause is the issue. It’s not to place blame but it’s to discover what happened so it can be prevented in the future. In looking at the possible causes I learned a lot about what not to do on a job site. Between knowing what to do and what not to do I will be a better asset to a job.
If you had a guy on a forklift dump a pallet of sub floor on two beams in the middle of a span and didn’t figure out what happened you’d do it again. I want someone that thinks and learns from mistakes.