Did you know that wood is the most sustainable, natural and renewable building material available in North America? Wood represents a building material that can assist in the fight against climate change caused by greenhouse gases. It is renewable, recyclable, reusable, and organic. It also cleans the air, cleans water, provides oxygen, and is biodegradable. Compared to many other components, it is strong, lightweight, flexible, diverse, attractive and easy to use.
Why opt for a wood-frame building?
In simply opting for a wood-frame residence instead of a concrete residence, you are assisting in the cleaning of the atmosphere! It is true! As trees grow, they help reduce climate change by absorbing and storing CO2 away. Wood helps reduce climate change when it is used instead of other more energy-intensive materials or as biomass energy instead of fossil fuels.
A typical 2400 square foot wood-framed house has over 28 metric tons of carbon dioxide sequestered within the wood building materials products used in the construction of the building. That is the equivalent to the Carbon Dioxide (C02) emissions from a single passenger car driven for seven years, or 3,300 gallons (12,500 liters) of gasoline burned, or the energy costs to operate the house for almost 4 years!
Discover how the TRIFORCE® open joist floor system can integrates in a Passive House project as explained by George Reefer, Construction Manager at Ecocor.
Build with an all-wood open-web joist
The TRIFORCE® is entirely made from engineered wood, without steel plates. The carbon footprint of wood is several times smaller than that of steel or concrete. Wood products in general use 60 times less energy to produce than steel products. Wood simply consumes much less fossil fuels in its manufacturing. Though a tree might take 60 years to regrow, that is nothing compared to the 500 million years it takes to reform the petroleum used in the manufacturing cycle of concrete or steel. Also, not using metal plates in TRIFORCE®’s design actually gives it better fire resistance.
Raw materials of the TRIFORCE® are kept to a minimum: Spruce-Pine-Fir (SPF) lumber, Oriented Strand Board (OSB) and a PRF adhesive. SPF lumber is sourced in Canadian forests managed for sustainability while OSB converts otherwise limited-use wood fiber to strong, engineered panels. And, the PRF adhesive used to assemble TRIFORCE® is an industry-standard stable ingredient resistant to water and high temperatures.
The wood comes from parts of trees that were traditionally considered wastes (unused black spruce tree tops, in our case). Engineered wood takes it a step further by primarily using wood that would have otherwise been thrown away in the process of creating lumber. If you look at the acquisition step of the wood manufacturing process, widely used traditional 2 x 10s or 2 x 12s are milled from larger trees than those needed for engineered wood, and the resulting deforestation is more impactful. Engineered wood on the other hand is made from a combination of adhesives and wood particles that can come from the smallest trees.
When the wood is processed, engineered wood products are particularly efficient: in the making of OSB, for example up to 90% of the raw material is put to use as a wood product. In the case of milled lumber, that number drops to 60% or less.
Choosing the open joist TRIFORCE® is making a green choice for generations to come. It is not only light to carry, always in stock, and trimmable on the jobsite! You can now add its ecological aspect as another reason to make the move and try it now!
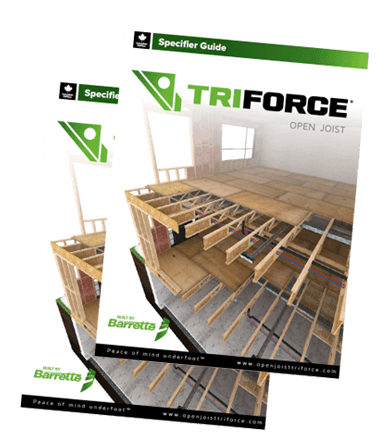
Do you have an online AIA Continuing Education course organized to educated dumb Architects?
Myatt
I would like to know more on this product