A high-performance floor system must be effective at all levels. Safety, comfort, cost optimization, practicality in construction. All being important considerations for both builders and owners. Discover five reasons why your floor system could be underperforming without you knowing it!
1. It is not fireproof
Depending on the construction type, the floor system must either be in compliance with Section R302.13 of the 2015/2018 IRC (equivalent fire-resistant construction to 2-inch-by-10-inch nominal dimension lumber) or, be built in accordance with an approved fire-resistant assembly for multifamily buildings.
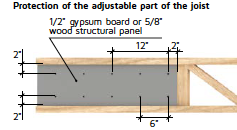
If your original (as-built) floor system was constructed properly, it shouldn’t require specific treatment with chemicals to meet fire prevention standards. These treatments can generate significant additional costs if not considered in the initial budget and the products used to treat the floors often release volatile organic compounds in the air several months (or even years) after their application.
2. It is not performing against vibration
Vibrations are very unpleasant in a home or even an office. They create a feeling of insecurity and discomfort or at a minimum, are an annoyance. A properly constructed floor system can keep vibrations to a minimum.
Well thought and assembled floor system allows a greater control over vibrations by simply adding strongbacks in strategic locations, amongst other strategies. Strongbacks help distribute weight evenly to adjacent joists. The resulting rigidity effectively dampens vibration.
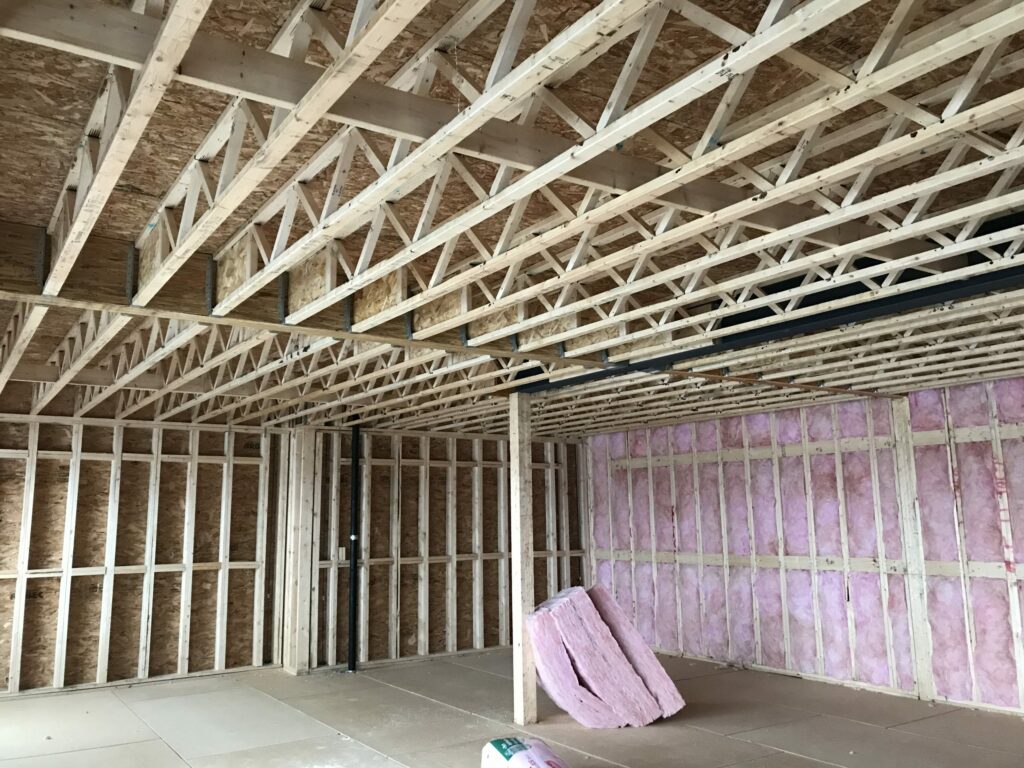
3. It is not silent
You should not hear your floor system. An underperforming floor squeaks when you walk on it, which can be unpleasant if one needs to be discreet! Floors can be noisy for several reasons: bad installation, bad materials or damage from time and usage.
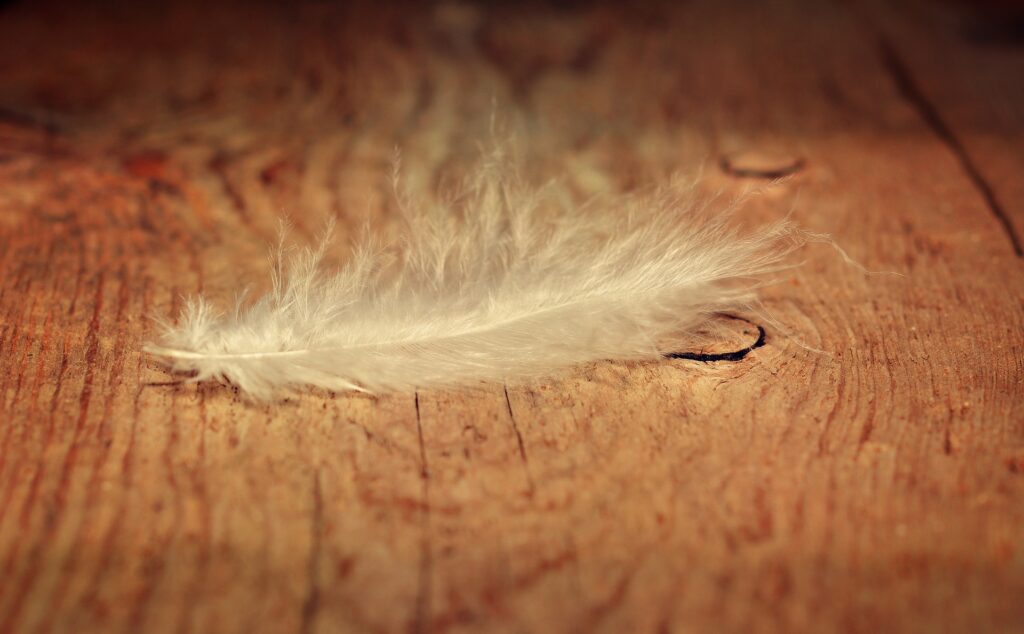
4. It is not time and cost effective
What if you had the whole flooring done, just to realize a couple of years later you would have wanted a water exit on the other side of the house? Or a new bathroom, and pipes and wires to get across the room? Or if you had an electrical failure, short circuit or leaky pipe to localize?
If you don’t work with open joists, you’d have to get the floor or ceiling opened all over again to get to your wiring or piping, or to get new equipment through. With an open joist design, the access to the space between floor and ceiling is much easier, reducing further renovation costs and complexity considerably.
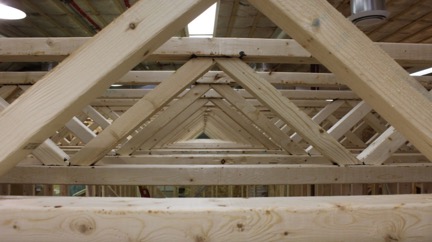
It’s a long term investment in your future projects!
5. It has not been tested
Not all manufacturers take the time and can afford to individually test every joist before it leaves the factory. In addition to offering peace of mind, the tests help to guarantee high-standards for product quality and durability that exceed market expectations.
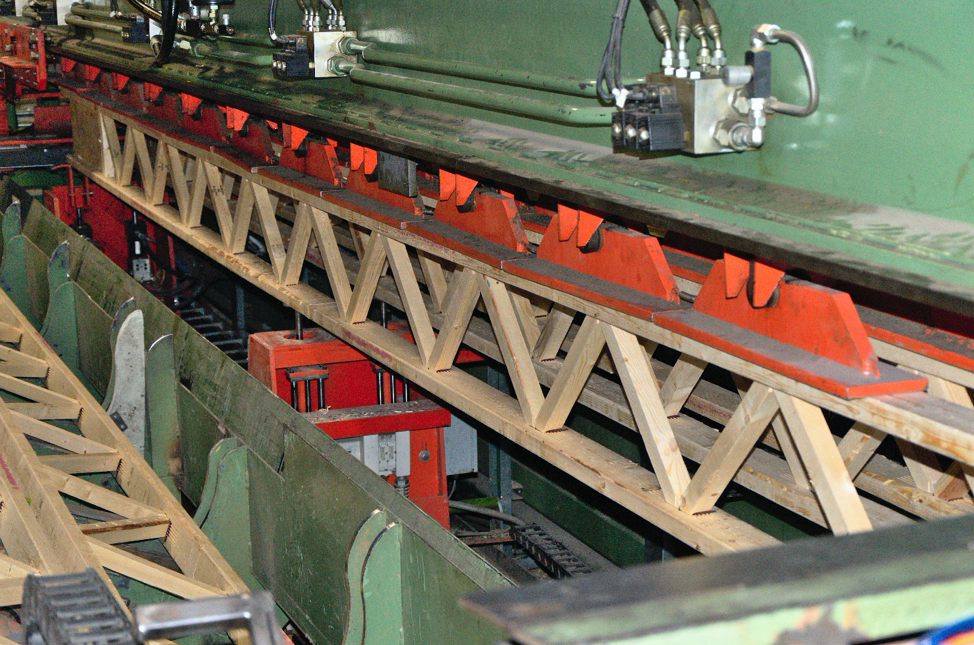
In other words, a well-performing floor system helps builders improve the quality of their work in all aspects: security, comfort and quality of life. Things that buyers and tenants notice and the things that improve a building’s value and longevity.
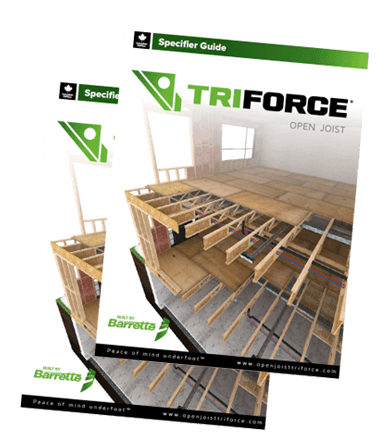